MCナイロン切削条件の基本と最適化方法
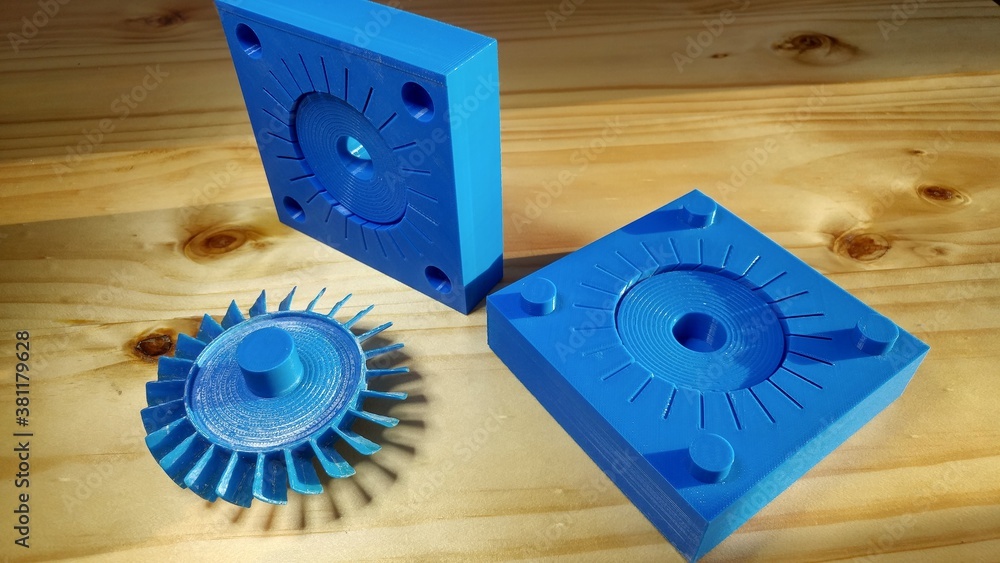
皆さんは「MCナイロンを加工したいけれど、切削条件が分からない……」というお悩みを抱えてはいませんか?その悩みを解決するために、私たちは「MCナイロン切削条件の基本と最適化方法」というガイドを作成しました。
この記事は、以下のような方々に向けています。
- MCナイロンとは何か、基本的な特性について知りたい方
- MCナイロンの切削条件を理解し、効率的な加工を行いたい方
- 切削条件を最適化して、より高い品質と生産性を追求したい方
- 加工現場で実践的に役立つ情報を求めている方
MCナイロンは、その優れた機械的特性と耐摩耗性から多くの産業で利用されており、正しい切削条件を理解することは非常に重要です。しかし、切削条件は材料や加工方法によって異なるため、最適な設定を見つけるのは一筋縄ではいきません。
この記事では、MCナイロンの基本的な特性から開始し、切削条件の設定方法や最適化のテクニックまでを詳しく解説します。これからの加工に役立つ知識を手に入れ、より良い成果を上げるための第一歩を踏み出しましょう!
1. MCナイロン切削条件の基本知識
1-1. MCナイロンとは?
MCナイロン(Modified Cast Nylon)は、鋳造法によって製造される高性能エンジニアリングプラスチックの代表格です。分子構造が高密度かつ均質であり、そのために優れた機械的強度、耐摩耗性、耐衝撃性を誇ります。一般的な用途としては、摺動部品やギア、ベアリング、機械の構造部材などが挙げられ、耐久性と精度が要求される場面での使用が多いです。
1-2. MCナイロンの特性
- 高い機械的強度と耐摩耗性
- 優れた耐衝撃性と靭性
- 吸湿率が低く寸法安定性に優れる
- 耐薬品性・耐熱性が高く、一般的な使用環境で100〜120℃まで耐える
- 切削加工が容易で高精度な加工が可能
2. MCナイロン切削条件の最適化技術
2-1. 切削速度の最適範囲
MCナイロンは熱に弱いため、切削中の発熱を抑えることが重要です。適切な切削速度は20〜40m/minが理想とされます。高速過ぎると材料が熱で軟化し、加工面に焼けや溶融が生じやすくなります。逆に低速すぎると工具の摩耗や切削効率の低下を招くため、最適速度の設定が不可欠です。
2-2. 送り速度の適正設定
送り速度は、刃物径や刃数に応じて0.05〜0.15mm/revを目安に調整します。適切な送り速度により、切削抵抗の安定化と加工面の滑らかさが向上します。過大な送りは表面粗さ悪化や工具損傷のリスクを高めるため、素材特性に合わせた制御が必要です。
2-3. 切削深さの制御
切削深さは0.5〜2.0mmの範囲が一般的です。過度な切削深さは工具への負担増加や加工変形を引き起こすため、複数回に分けた段階的加工を推奨します。特に精密部品では、仕上げ段階で浅い切削深さにより微細な仕上げを行い、寸法精度と表面品質を確保します。
2-4. 冷却剤の活用
熱蓄積を防ぎ、加工面の品質を維持するために、切削加工時は適切な冷却剤(主に水溶性クーラントやエアブロー)を使用します。ただし、吸湿性のあるMCナイロンの場合、過剰な水分は寸法変化の原因となるため、使用量と方法を適切に管理することが重要です。
3. 青色MCナイロンの特性と推奨加工条件
3-1. 青色MCナイロンの特徴
青色MCナイロンは、顔料や特殊添加剤を配合することで、耐摩耗性や外観の安定化を図った材料です。顔料の影響により、熱伝導性や機械的性質が標準品と微妙に異なる場合があり、加工時に若干の注意を要します。特に色むらや熱変質が起こりやすいため、切削条件の最適化が不可欠です。
3-2. 推奨加工上のポイント
- 切削速度はやや低めに設定(15〜30m/min推奨)し、熱の蓄積を抑制する。
- 冷却はエアブローや微量の水溶性クーラントを活用し、過剰な水分による寸法変化を防ぐ。
- 刃物は超硬エンドミルなど鋭利で熱伝導に優れた工具を使用し、加工熱の発生を抑える。
- 定期的な工具交換とメンテナンスを行い、加工精度と表面品質を維持。
- 仕上げ段階では浅い切削深さでの多段階加工を推奨し、色ムラや表面粗さを最小限に抑える。
MCナイロンおよび青色MCナイロンの切削加工は、材料特性を正確に把握し、温度管理・工具管理・加工パラメータの最適化を徹底することで、高精度かつ高品質な製品を生み出せます。特に熱に弱い点を考慮した冷却と切削条件の制御が、加工成功の鍵となるでしょう。
4. MCナイロン加工の高度ポイントと実践事例分析
4-1. 卓越した加工事例の詳細紹介
MCナイロンは耐摩耗性、耐衝撃性、自己潤滑性に優れ、精密部品から耐久部品まで多様な分野で活用されています。特に精密ギアや摺動部品においては、寸法安定性と耐摩耗性が求められ、高速回転機械でも高い信頼性を発揮しています。例えば、自動車のパワートレイン部品においては、MCナイロンの加工精度と強度を活かし、金属部品に匹敵する耐久性能を実現した事例が数多く報告されています。また、医療機器分野では非毒性と耐薬品性を活かした部品加工も成功例として挙げられます。
4-2. 成功事例に学ぶ高度加工の要諦
MCナイロン加工の成功は、材料物性に基づいた高度な加工管理とノウハウの蓄積に依存します。主なポイントは以下の通りです。
- 切削パラメータの精緻な制御:切削速度、送り速度、切込み量を材料特性と形状に応じて最適化し、熱変形と応力集中を抑制。
- 高精度工具の使用とメンテナンス:超硬エンドミルやコーティング刃物を活用し、刃先の摩耗を最小限に抑える。
- 段階的切削による負荷分散:一発で深く削るのではなく、粗加工から仕上げまで段階的に切削。これにより加工応力の低減と表面品質の向上を両立。
- 冷却・潤滑管理の徹底:適切な冷却剤やエアブローによる温度管理で熱影響を低減し、材料の変形や焼き付きを防止。
- 加工後の応力解放処理:熱や機械的応力による残留応力を緩和し、反りや寸法変動を抑制する工程の導入。
これらを体系的に実施することで、高精度かつ高耐久なMCナイロン部品の量産が可能となっています。
5. MCナイロン切削・フライス加工の全工程マニュアル
5-1. 加工前の徹底した準備
MCナイロンの加工では、材料の吸湿状態が品質に直結するため、保管時の湿度管理と加工前の含水率測定が必須です。また、加工機械や切削工具は材料特性にマッチした仕様を選定。特に超硬エンドミルは刃先の形状、コーティング材質、刃数を考慮し、加工条件に最適化します。さらに、冷却システムやエアブロー装置の準備を入念に行い、加工時の熱蓄積を防ぎます。
5-2. 高精度切削・フライス加工の詳細手順
- 粗加工段階
- 切削深さは1.5〜2.0mm程度とし、過度な切削抵抗を避けるため切削速度は中程度に設定。
- エアブローやクーラントの使用で熱の局所的蓄積を防止。
- 中仕上げ段階
- 切削深さと送り速度を適切に減少させ、表面粗さの改善に注力。
- 刃物の摩耗を確認し、必要に応じて工具交換。
- 仕上げ加工段階
- 切削深さを0.2〜0.5mmに制限し、送り速度も最小限に設定。
- 冷却剤の適切な供給で材料の熱変形を防ぎながら、精密な寸法管理を実現。
- 工具メンテナンス
- 定期的に刃先の摩耗度合いを計測し、切れ味の低下を即時に補正。
5-3. 加工後の仕上げと品質検査
加工終了後は、熱や応力による反りを最小限に抑えるために自然乾燥または低温乾燥炉による含水率の安定化処理を実施。バリ取りは高精度な手法で行い、表面を滑らかに整えることで機械的性能を最大限に発揮します。寸法検査は三次元測定機(CMM)や高精度マイクロメーターで厳密に実施し、製品の許容誤差内を厳守。さらに、耐摩耗性や耐荷重性の試験を行い、品質保証体制を確立しています。
MCナイロン加工は、単なる切削技術にとどまらず、材料特性の深い理解と高度な加工管理を統合することで、耐久性と高精度を両立した製品づくりが可能となります。工程ごとに厳密な品質管理とノウハウを蓄積し続けることが、長期的な競争力確保の鍵となります。
まとめ
MCナイロンの切削条件は、工具の材質、切削速度、送り速度、切削深さが重要です。最適化には、これらの要素を調整し、加工の目的や材料特性に応じた試行錯誤が必要です。適切な条件を見つけることで、加工精度や表面品質を向上させることが可能です。