MCナイロンの加工方法完全ガイド!初心者でもわかる切断テクニック
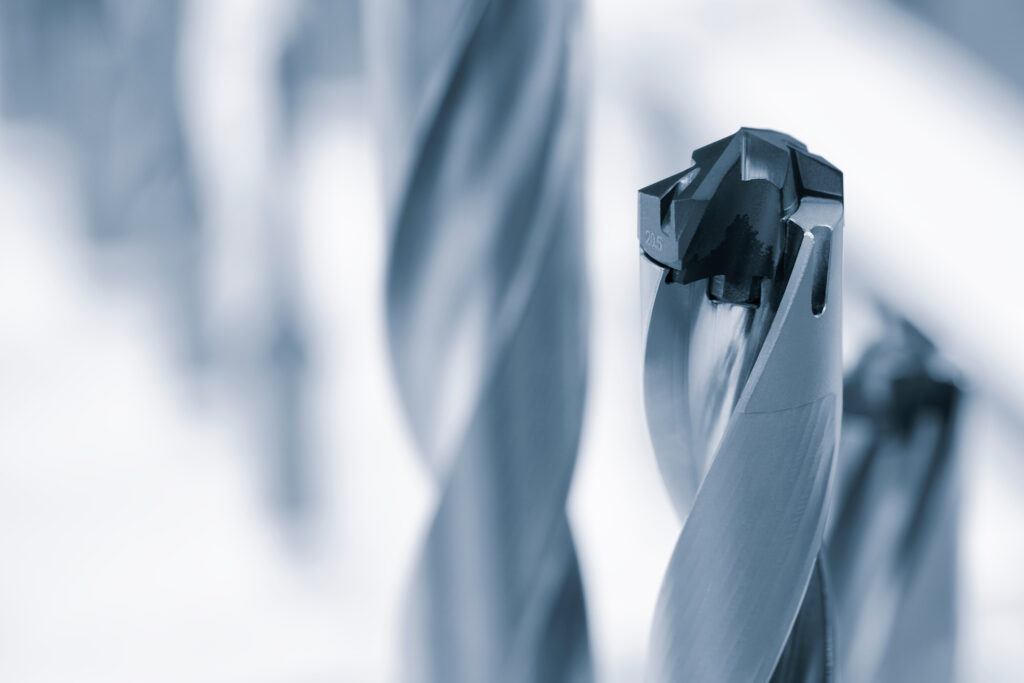
MCナイロンは、様々な産業で利用される優れた素材であり、その加工方法を理解することは重要です。初心者でもわかるように、MCナイロンの切断テクニックを詳しく解説した完全ガイドがこちらにあります。MCナイロンの特性や適した工具、正しい手順など、加工に必要な全ての情報をご紹介します。加工技術の向上に役立つヒントやコツもありますので、ぜひ読み進めてください。MCナイロンに関する知識を深め、自信を持って加工作業に取り組んでみましょう。
MCナイロンとは
MCナイロンは、ナイロン6を基にした高性能なエンジニアリングプラスチックの一種です。正式には「メルセンナイロン」とも呼ばれ、その優れた物理的特性や化学的耐性から、さまざまな産業で使用されています。特に機械部品や摩耗の激しい部品に使用されることが多いです。MCナイロンの基本知識
MCナイロンは、ナイロン6の樹脂を特殊な方法で加工し、自己潤滑性や高耐摩耗性を持たせた材料です。この加工方法により、MCナイロンは非常に高い強度と耐久性を持ち、さまざまな厳しい環境下でも安定した性能を発揮します。- 主成分: ナイロン6(ポリアミド)
- 物理的特性: 高い引張強度、耐摩耗性、耐衝撃性
- 化学的特性: 耐薬品性、耐油性、耐熱性
MCナイロンの特性と利点
MCナイロンには、多くの特性があり、これがさまざまな分野での利用を可能にしています。以下はその主要な特性と利点です。1. 耐摩耗性
MCナイロンは非常に高い耐摩耗性を誇り、摩擦が大きい環境での使用に非常に適しています。これにより、摩耗しやすい機械部品に長寿命を与えます。2. 自己潤滑性
特に、MCナイロンは摩擦を軽減するための自己潤滑機能を持っています。これにより、油や潤滑剤を使用せずに運転可能で、コスト削減や環境負荷の低減にも寄与します。3. 高強度と耐衝撃性
MCナイロンは引張強度が高く、衝撃にも強いので、過酷な機械的負荷がかかる部品に適しています。4. 耐薬品性と耐熱性
耐薬品性や耐熱性も高いため、化学薬品や高温の環境下でも安定して使用できます。MCナイロンの用途と応用分野
MCナイロンは、耐摩耗性や自己潤滑性を生かしてさまざまな分野で利用されています。代表的な用途は以下の通りです。1. 機械部品
- ギアやベアリング: 高い耐摩耗性により、ギアやベアリングの部品に最適です。
- 歯車やプーリー: 摩擦や衝撃に耐えるため、歯車やプーリーに広く使用されています。
2. 自動車産業
- エンジン部品: 高強度と耐熱性を活かして、エンジン部品や冷却システム部品にも使用されています。
- バンパー部品や内装部品: 自動車の外装や内装にも耐久性の高いMCナイロンが使用されています。
3. 食品業界
- 食品加工機器部品: 高い耐薬品性を活かし、食品加工機器の部品にも使われます。
4. 電子機器
- コンデンサーやスイッチ部品: MCナイロンは電子機器の小型部品にも利用されています。
5. 建設業
- クレーンや建設機械の部品: 高耐摩耗性が求められる建設機械の部品にも利用されています。
MCナイロンの加工前の準備
MCナイロンはその優れた特性を活かすために、適切な加工方法と準備が必要です。加工前の準備段階では、選定、工具の準備、安全対策、加工環境の整備が重要なポイントとなります。ここでは、それぞれのポイントについて詳しく解説します。加工するMCナイロンの選定
MCナイロンの加工において最初に重要なのは、使用するMCナイロンの種類と規格の選定です。加工方法によって適切な素材が異なるため、以下の要素を考慮して選定します。- 形状とサイズ: 加工する部品の形状やサイズに応じて、適切な厚さや長さのMCナイロンを選びます。
- 物理的特性: 部品がどのような負荷を受けるか(摩耗、衝撃、熱など)に基づいて、特性に合った材料を選びます。例えば、高摩耗部品には特に高い耐摩耗性を持つMCナイロンを選定します。
- 加工方法: 切削加工や圧縮成型など、使用する加工方法に合った規格のMCナイロンを選ぶことが重要です。
加工方法の選定基準
- 高精度を要求する場合は、精密加工用のMCナイロンを選ぶ。
- 大型部品を製作する場合、規格外の大きなサイズを選定することが多い。
必要な工具と安全対策
MCナイロンは硬度が高く、加工中に高温が発生することもあるため、適切な工具と安全対策を整備することが求められます。以下の工具と安全対策が推奨されます。必要な工具
- 旋盤とフライス盤: MCナイロンを切削するためには、精密な切削工具が必要です。特に旋盤やフライス盤はよく使用されます。
- ドリルとタップ: 穴あけやネジ切りには専用のドリルやタップを使用します。ナイロン専用の切削工具を使うことで、作業がスムーズに進みます。
- バリ取り工具: 加工後のバリを除去するための工具が必要です。
安全対策
- 作業服と手袋: MCナイロンの切削時には、切削チップや破片が飛散するため、適切な作業服と保護手袋を着用します。
- 目の保護: 目の保護が必要です。特に切削中のチップが目に入らないよう、安全メガネを着用します。
- 換気設備: 加工時に発生するガスや微粒子を排出するため、換気を徹底する必要があります。
加工の際の注意点
- MCナイロンは切削時に熱を発生しやすいため、冷却剤やエアーによる冷却を行うことが推奨されます。
- 適切な切削速度を選定し、過度な熱の発生を防ぐことが重要です。
加工環境の整備
MCナイロンの加工を行う環境も非常に重要です。加工環境が整っていないと、製品の精度や品質が低下することがあります。環境の整備
- 作業台や機械の清掃: 作業台や使用する機械が清潔であることが前提です。切削時のゴミや粉塵が機械の動作に影響を与えることがあるため、定期的な清掃が必要です。
- 適切な温度管理: MCナイロンは温度変化に敏感なため、加工環境の温度を安定させることが重要です。温度が極端に変動すると、素材の特性が変化することがあります。
- 照明の確保: 加工中に視認性を確保するため、適切な照明が必要です。精密な加工が求められるため、十分な照明を確保します。
作業エリアの整理
- 加工用具や工具は使用後に整理し、必要なものがすぐに取り出せるようにすることで効率的な作業ができます。
- 作業中の安全を確保するため、作業スペースの確保や事故防止のための標識を設置することも有効です。
加工における温度と湿度の管理
- MCナイロンは温度や湿度の変化により膨張することがあります。そのため、一定の温度と湿度を保つことで、安定した加工が可能になります。
MCナイロンの切断テクニック
MCナイロンはその強度と耐摩耗性が特徴ですが、適切な切断方法を選ばないと、切断面が不安定になったり、精度が低下したりすることがあります。ここでは、MCナイロンを切断するためのテクニックについて、切断条件の理解から手動、機械切断方法、切断時の注意点まで解説します。切断に適した条件の理解
MCナイロンを切断する際、素材特性に合った条件で作業を行うことが大切です。以下の条件を理解し、最適な切断方法を選ぶことが重要です。- 切断速度: MCナイロンは比較的軟らかい素材ですが、過度な切断速度では熱が発生し、変形や溶ける原因になります。切断速度は遅めに設定し、安定した切断を心がけましょう。
- 冷却剤の使用: 切断中に発生する熱を抑えるため、冷却剤やエアーを使用することが推奨されます。冷却剤がない場合は、エアーで冷却しながら作業を進めると良いでしょう。
- 切断工具の選定: MCナイロンを切断するためには、専用の工具が必要です。刃先が鋭いものを選び、摩耗を最小限に抑えることが求められます。
手動切断方法
MCナイロンの手動切断方法は、主に以下の方法で行われます。1. ノコギリによる切断
- 使用する道具: MCナイロン用の細かい歯のノコギリを使用します。
- 手順:
- 切断する位置に定規を合わせてマーキングをします。
- ノコギリでゆっくりと均等に切断します。
- 切断面にバリが出ることがあるので、バリ取りを行い、滑らかに仕上げます。
2. 手動カッター
- 使用する道具: MCナイロン専用の手動カッター(例えば、プラスチック用のカッター)を使用します。
- 手順:
- 切断面をマーキングします。
- 手動カッターで一定の力を加えながら、少しずつ切り進めます。
- 切断後、バリ取りを行います。
機械切断方法
機械切断は、手動切断よりも精度が高く、効率的に作業を進めることができます。以下の方法が一般的です。1. 旋盤による切断
- 使用する道具: 旋盤、MCナイロン専用の刃物(切削工具)を使用します。
- 手順:
- MCナイロンを旋盤にセットし、安定させます。
- 切断工具で慎重に回転しながら切断します。
- 切断中に冷却剤を使用し、熱を抑えながら作業を進めます。
2. フライス盤による切断
- 使用する道具: フライス盤、MCナイロン専用のカッターを使用します。
- 手順:
- MCナイロンをフライス盤にセットします。
- スピードや切削条件を調整し、フライス盤で切断を行います。
- 切断後、バリ取りと表面処理を行います。
3. 糸ノコ盤による切断
- 使用する道具: 糸ノコ盤、MCナイロン専用のノコギリを使用します。
- 手順:
- MCナイロンを糸ノコ盤にセットします。
- 軽い力で切断を開始し、必要に応じてスピードを調整します。
- 切断後、表面が滑らかになるよう仕上げます。
切断時の注意点
MCナイロンを切断する際には、いくつかの重要な注意点があります。1. 熱の管理
MCナイロンは熱を持ちやすく、過度な温度上昇が素材を溶かす原因となることがあります。切断中は冷却剤を使用したり、エアーで冷却しながら作業を行うと良いでしょう。2. バリ取り
切断後には必ずバリが発生します。バリをそのままにしておくと、後続の加工に支障をきたすことがあるため、バリ取りをしっかり行い、滑らかな仕上げを目指します。3. 切断角度の管理
切断時に角度がずれると、精度が落ちるだけでなく、部品同士が正しく合わさないことがあります。正確な切断角度を保つよう心掛けましょう。4. 適切な工具の使用
MCナイロンを切断する際には、専用の工具を使用することが大切です。特に鋭利で高品質な工具を使用することで、より良い仕上がりが得られます。5. 安全対策
切断中のチップや破片が飛散する可能性があるため、適切な保護具(安全メガネ、手袋、作業服)を着用し、安全対策を講じることが必須です。切断後のMCナイロンの仕上げ
MCナイロンの切断後は、端面の処理や表面の仕上げを行うことで、部品の精度や耐久性を高め、仕上がりを美しく整えることができます。ここでは、切断後に行うべき端面の処理、熱処理、表面の仕上げ方法について詳しく解説します。端面の処理
切断後の端面は、バリや不均一な仕上がりが発生しやすいため、きれいに整える必要があります。端面処理を行うことで、部品の性能が向上し、使用中の摩耗を抑えることができます。1. バリ取り
- 方法: バリ取りには、ナイフやデバリングツールを使用します。バリ取りは切断面が滑らかでない場合に行い、バリを完全に除去することが重要です。
- 手順:
- 切断面のバリを目視で確認します。
- ナイフやデバリングツールを使い、丁寧にバリを削り取ります。
- 仕上げ後、再度チェックしてバリが完全に取れているかを確認します。
2. 面取り
- 方法: 面取りは、角を丸く削ることで、部品が他の部品と接触する際の摩耗を減少させ、ケガ防止にも役立ちます。
- 手順:
- 面取り用の工具(例えば、バリ取り工具やサンダー)を使用します。
- 角を適切な角度で削り、滑らかな仕上げを施します。
熱処理と応力除去
MCナイロンは切断後に内部応力が残ることがあり、これが原因で部品が変形する場合があります。熱処理と応力除去を行うことで、部品の安定性を高めることができます。1. 熱処理
- 目的: 熱処理は、MCナイロンの内部応力を減少させ、部品が安定することを目的としています。また、熱処理を施すことで、素材の機械的特性を改善することもできます。
- 手順:
- MCナイロンを一定の温度に加熱します(通常、約80〜100度)。
- 適切な時間だけ加熱した後、冷却します。このプロセスを繰り返すことで、内部応力が軽減されます。
2. 応力除去
- 方法: 応力除去は、冷却後に部品を一定期間放置することで行います。この過程で、MCナイロンは安定し、変形のリスクが減少します。
- 手順:
- 切断後にMCナイロンを自然冷却し、数時間放置します。
- 必要に応じて、さらに冷却または温度変化を繰り返して安定させます。
表面の仕上げ方法
MCナイロンの表面を滑らかに仕上げることで、外観が向上し、使用中の摩耗が減少します。表面仕上げにはいくつかの方法があります。1. サンディング(研磨)
- 方法: 研磨は、表面を平滑にし、傷や凹凸を除去するための基本的な手法です。サンドペーパーや研磨機を使用して、表面を滑らかに仕上げます。
- 手順:
- 表面にサンドペーパーを使い、粗い目から順に細かい目に変更して研磨します。
- 研磨後、表面が均一に滑らかになったことを確認します。
2. ツルツル仕上げ(ポリッシング)
- 方法: ポリッシングは、さらに光沢を持たせる仕上げ方法で、最終的に光沢のある美しい表面を得ることができます。
- 手順:
- ポリッシャーや研磨剤を使用して、表面に均一に磨きをかけます。
- 丁寧に研磨を進め、最終的に艶のある滑らかな表面に仕上げます。
3. 化学的仕上げ(研磨液や溶剤を使用)
- 方法: 特定の化学薬品や溶剤を使用することで、表面の微細な傷を除去し、より滑らかに仕上げることができます。特に大面積を仕上げる場合に有効です。
- 手順:
- 研磨液や溶剤を表面に均等に塗布します。
- 指示された時間、溶剤が反応するのを待ち、表面を洗浄します。
切断以外のMCナイロン加工方法
MCナイロンは非常に多用途で、切断だけでなく、様々な加工方法が存在します。ここでは、穴あけ加工と熱成形加工に焦点を当て、それぞれの加工方法について詳しく解説します。穴あけ加工
MCナイロンに穴を開ける際には、特に精度と仕上がりを重視する必要があります。適切な工具と加工条件を選定することで、効率よく綺麗な穴を開けることができます。1. 穴あけのための工具選定
- ドリル: MCナイロンの穴あけには、通常の金属加工用ドリルでも問題なく使用できますが、鋭利な先端を持つドリルビットを選ぶことが重要です。
- ピンバイスやボール盤: 精度を必要とする場合は、ピンバイスやボール盤を使用することで、高精度な穴あけが可能です。
2. 穴あけのポイント
- 適切な回転数: 高速回転を避け、MCナイロンを過熱しないように注意が必要です。中程度の回転数で加工することが推奨されます。
- 冷却と潤滑: 穴あけの際には、加工温度が上がりやすいため、冷却や潤滑を行うことで、摩擦を減らし、切削面を滑らかに保つことができます。専用の切削油や水を使用することが有効です。
- ドリル角度の確認: ドリルの角度は重要で、MCナイロンでは直線的で均一な穴あけを行うため、適切な角度を持つドリルを使用します。
3. 穴あけ後の仕上げ
- バリ取り: 穴を開けた後、バリが発生することがありますので、バリ取りを行い、滑らかなエッジを作成します。
- 検査: 穴の位置や直径を確認し、仕様通りに加工できているかを検査します。
熱成形加工
MCナイロンは熱を加えることで、一定の温度で柔軟になり、成形が可能になります。熱成形加工を利用することで、複雑な形状を作ることができます。1. 熱成形加工の基本
- 加熱温度: MCナイロンを熱成形する際、適切な温度で加熱することが重要です。通常、140〜160℃が最適な範囲です。それ以上の温度になると、素材が溶けてしまうため、注意が必要です。
- 成形方法: 加熱したMCナイロンは、型に合わせて成形されます。型を用意し、加熱したMCナイロンをその型に押し込むことで、所定の形状に加工できます。
- 冷却: 成形後は、徐々に冷却して形状を固定します。冷却過程では、急激な温度変化を避け、均等に冷却することが求められます。
2. 熱成形の適用例
- カバーやシェルの製作: 複雑な形状を作る必要があるカバーやシェルの製作において、熱成形は非常に効果的です。
- パーツの弯曲: MCナイロンは熱で柔らかくなる特性を活かし、パーツの曲げ加工にも利用されます。
3. 熱成形時の注意点
- 過熱による変形: 熱成形時に過度な加熱を避けることで、MCナイロンが溶けることを防ぎ、変形を最小限に抑えることができます。
- 均等な加熱: 熱を均等に加えることで、成形後の精度や形状が安定します。
- 冷却の管理: 加工後は急冷を避け、MCナイロンが変形しないように冷却を行います。
MCナイロン加工時のトラブルシューティング
MCナイロンの加工中には、さまざまなトラブルが発生する可能性があります。これらの問題を早期に認識し、適切に対処することで、より良い加工結果を得ることができます。以下に、一般的な問題とその解決方法、そして加工精度を高めるためのコツを紹介します。切断時の一般的な問題
1. 切断面のバリ
- 問題: MCナイロンを切断するとき、端面にバリが発生することがあります。これは、切断時に高温や圧力が加わることで、素材の一部が変形してしまうことが原因です。
- 対策:
- 切断後にバリ取りを行い、仕上げ処理をすることで対処できます。
- 切断前に切断条件を見直し、適切な回転数と送り速度を設定することでバリの発生を最小限に抑えます。
2. 切断面が粗くなる
- 問題: 切断面が粗くなる原因は、適切な工具を使用していないことや、切断条件が合っていないことです。また、切断速度が速すぎると、切断面が滑らかになりません。
- 対策:
- 切断工具を定期的に確認し、摩耗している場合は交換します。
- 適切な回転数と送り速度を設定し、切断温度が上がりすぎないように注意します。切削油や冷却液を使用することで、摩擦を減らし、切断面を滑らかに保つことができます。
3. 材料の割れ
- 問題: MCナイロンは硬くて脆いため、切断時に割れてしまうことがあります。特に鋭利な工具で無理に切断を行うと、材料が割れることがあります。
- 対策:
- 切断工具の選定を慎重に行い、MCナイロンに適した切断方法を選びます。
- ゆっくりとした速度で切断を行い、過度な圧力を避けます。
- 冷却を行い、温度上昇を防ぐことで割れを防止します。
加工精度を高めるコツ
1. 適切な工具の選定
- コツ: 精度の高い加工を行うためには、MCナイロンに最適な工具を使用することが重要です。特に切削工具の刃先が鋭利であることが精度向上に寄与します。工具の選定にあたっては、刃先角度や素材との相性を考慮してください。
2. 加工条件の調整
- コツ: MCナイロンは温度変化に敏感な素材であるため、加工条件の調整が精度を高めるポイントとなります。特に、回転数や送り速度を適切に設定し、温度の上昇を防ぐことが大切です。また、湿度や冷却の管理も重要です。
3. クランプの確認
- コツ: 加工中に材料が動くと、加工精度が落ちる可能性があります。材料をしっかりとクランプし、動かないように固定することが、精度向上のカギとなります。
4. 微調整を行う
- コツ: 加工中に精度が低下した場合は、工具や加工条件の微調整を行いましょう。特に、送り速度や深さを細かく調整することで、仕上がり精度を高めることができます。
5. 定期的なチェックとメンテナンス
- コツ: 加工精度を維持するためには、工具の定期的な点検や機械のメンテナンスが欠かせません。定期的にメンテナンスを行い、問題が発生する前に予防することが、長期的な精度向上に繋がります。